Gantry
The gantry is known as a platform straddles the bed and maintain the motion of router spindle steadily. The gantry is usually constructed from tubular steel with reinforcing ribs welded throughout the length of the column which results in a steady firm beam assembly. Hence, it can help to minimize the vibration of cutter during cutting process. The movement along the bed is guided by the bearing rails and ball screw and controlled by the controller.
Table

T-slot and strap clamp
Multi-zoned table surface
The table of the machine is made from heavy duty tubular steel frame that is welded, precision machined and stress relieved so that the foundation remains true and steady over the operational life of the machine. The table is used to support the spoil board and T-slots. The spoil board allows the cutter to cut past its surface and not become damaged on worktable while T-slot can be used together with strap clamp to clamp the job to the spoil board.
The table surface is multi-zoned. Hence, it is easily switch from full sheet processing to smaller part processing if necessary. CNC router machine using suction method to ensure the workpiece fix in its position. The part is sealed against the table surface and the air inside the seal is removed using a vacuum pump. This method can prevent workpiece from distort during cutting process occurs.
Vacuum Pump
There are several types of pumps available for use with a CNC router machine and all have varying specifications. For example,
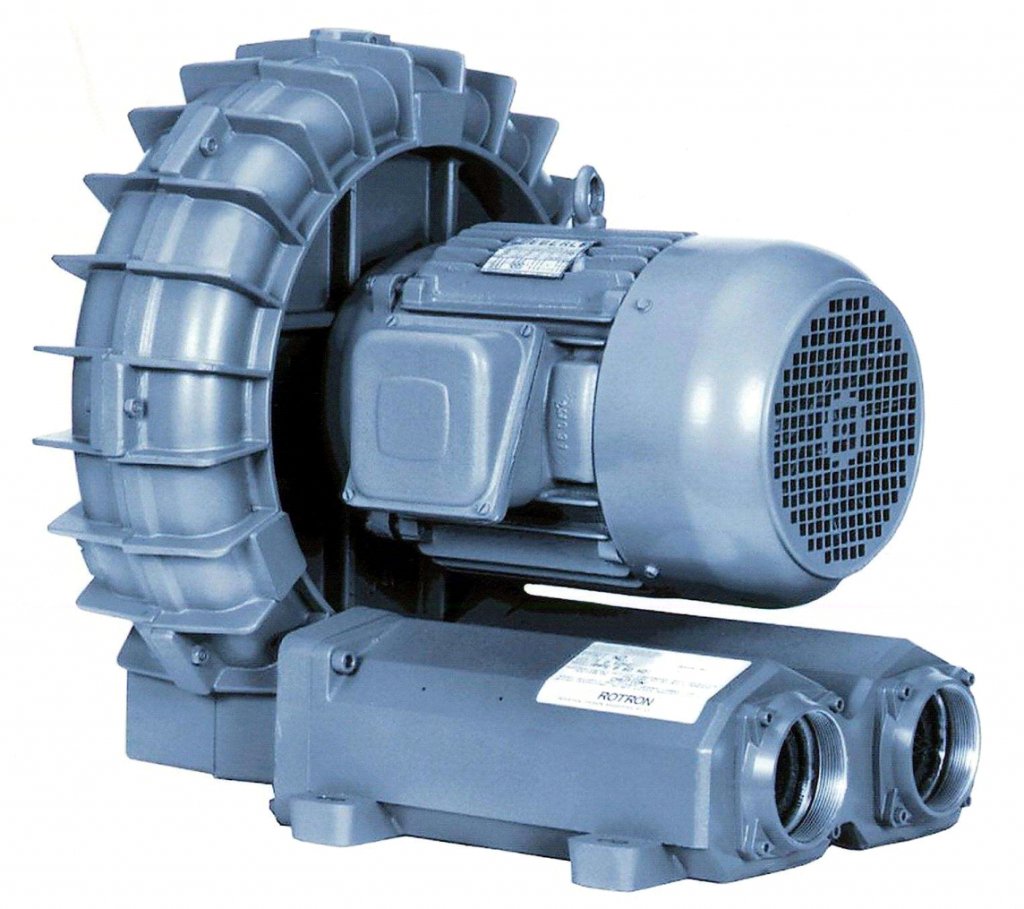
Regenerative Blower
Regenerative blower is typically a centrifugal type vacuum pump. It is suitable for cut parts that are generally quite large. These pumps use a rotating impeller to create a vacuum in order to move fluid. The pump’s impeller rotates within the housing and reduces pressure at the inlet. This motion will increases the pressure and send it out to discharge.
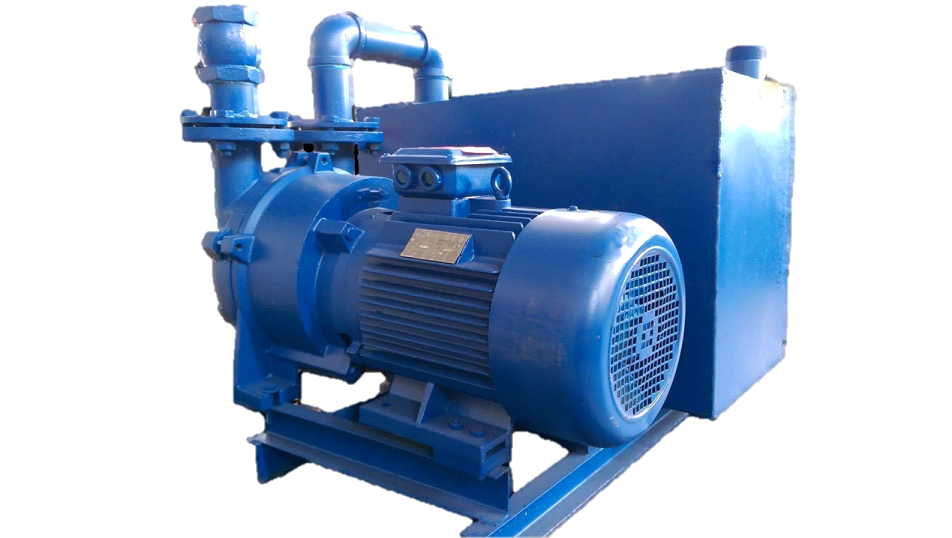
Water Vacuum Pump
This type of pump is suitable for pumping the gases. Furthermore, it can maintain its performance although in the bad working conditions such as large water discharge and load impact fluctuation.These pumps are usually used to pump the gas without solid particle,undissolved and noncorrosive gas in order to obtain vacuum in sealed vessels.
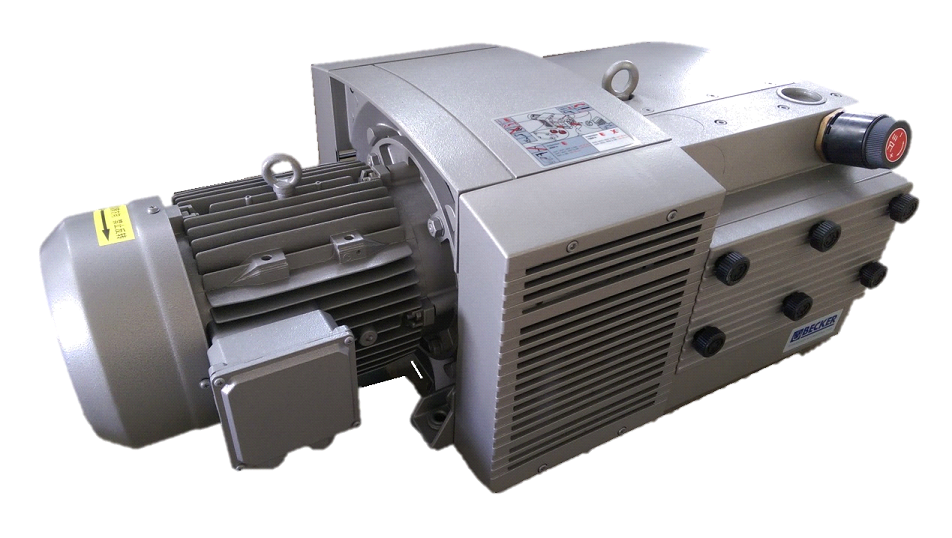
Rotary Vane Oil-less Vacuum Pump
Rotary vane vacuum pumps consist of electric motor coupled via belt or direct drive to the vacuum pump impeller. The vanes rotate in the pump housing, drawing air in the inlet and discharging the air through the exhaust, creating vacuum. When the vacuum is high, it will create superior hold-down capability and is ideal for wood, plastic, and other nonporous sheet-like materials. Example of this type of vacuum pump is Germany Becker Vacuum Pump.
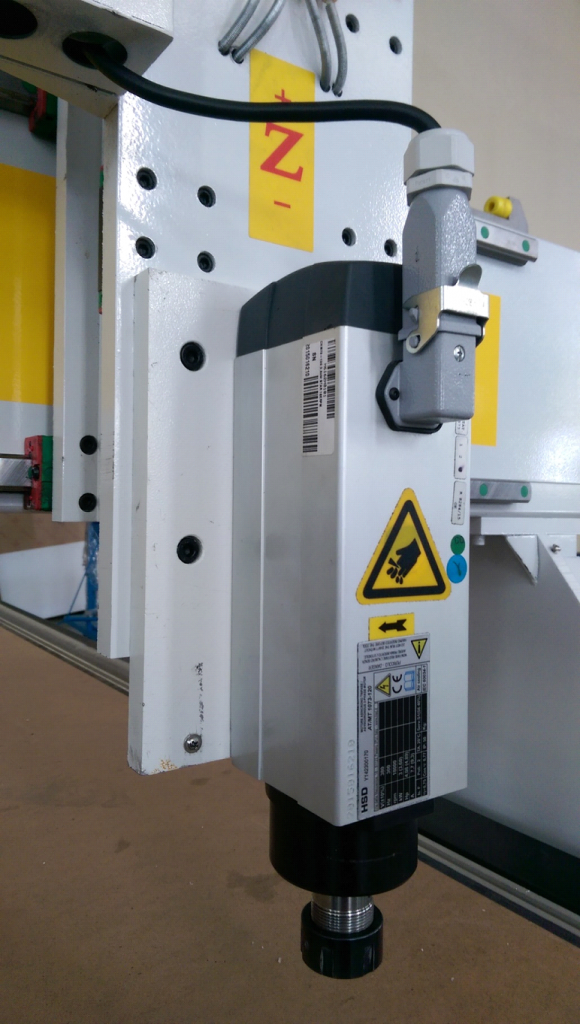
Router Spindle
The router spindle is very high precision. It is moved in the Z-axis by precision ball screw system while for X and Y-axis are the motion of rack and pinion. These two elements are controlled by the machine controller.
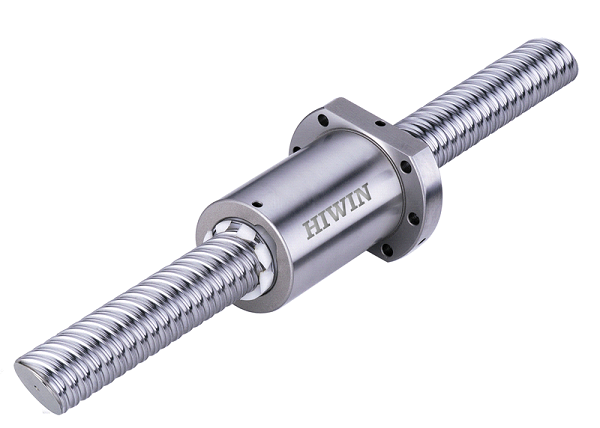
Ball Screw
Ball screw consists of a screw spindle and a nut integrated with rolling elements that cycle through a return mechanism. It is a linear actuator that translates rotational motion to linear motion. The ball screw can install on each of the three axis and is driven by stepper motor and move the spindle in X, Y and Z direction.
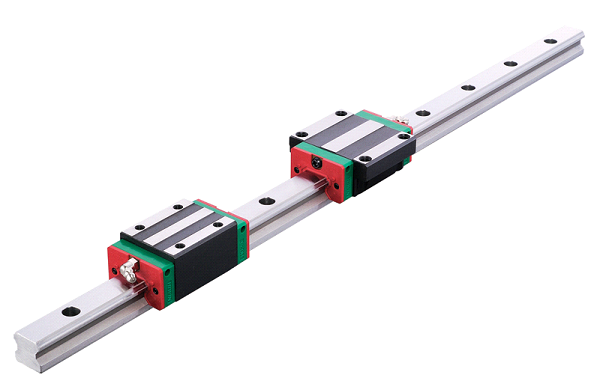
Linear Guideway
Linear guideway provides linear motion that utilizes re-circulating rolling elements between a profiled rail and a bearing block. The coefficient of friction on a linear guideway is only 1/50 compared to a traditional slide and are able to take loads in all directions. With these features, a linear guideway can achieve high precision and greatly enhanced moving accuracy.
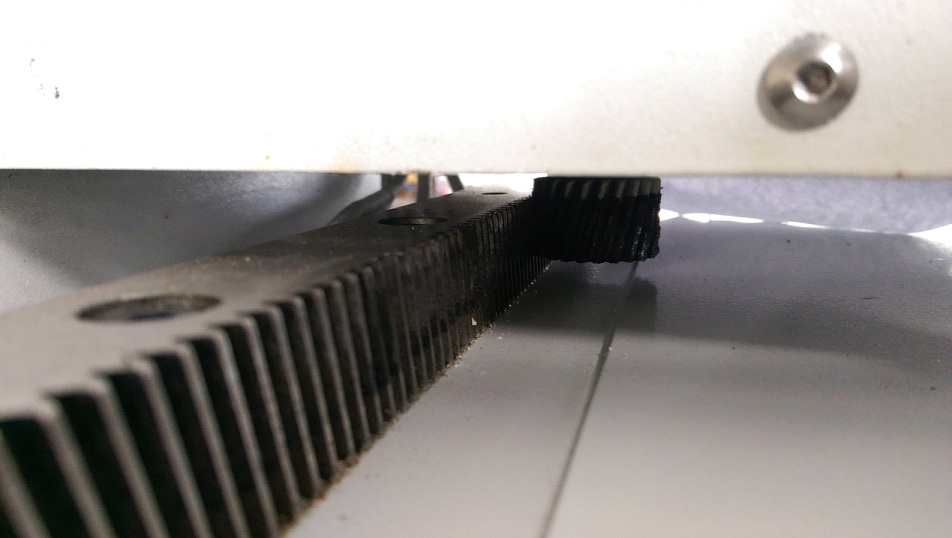
Rack and Pinion Drive
Rack and pinion is a linear actuator that consists of a pair gears. The rotational motion applied to the pinion causes the rack to move relative to the pinion, thereby translating the rotational motion of the pinion into linear motion. It is used in long-travel applications such as machine tool table positioning which require high stiffness and accuracy.
Driver System
Type of motor that commonly used is servo motor and stepper motor. The basic difference between a stepper motor and a servo motor is depends on how it is controlled and the system used.
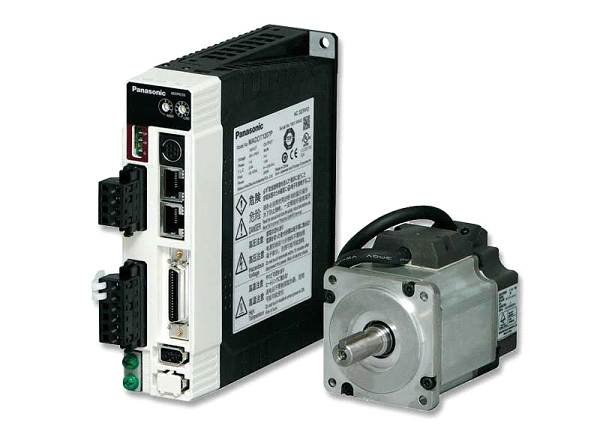
Servo motors are basically an assembled of four components, which are DC motor, gearing set, control circuit and position-sensor. Servo motor is a closed loop system. It will read the difference between the encoder and the commanded position and adjusts the current required to move. Servos only use few poles, usually between 4 to 12 poles, each pole offers a natural stopping point for the motor shaft. A pole is an area of a motor where a North or South magnetic pole is generated either by a permanent magnet or by passing current through the coils of a winding. This is because servo motors often requiring a position encoder to keep track of the position of the motor shaft, especially if precise movements are required. Servo motors are designed for more specific tasks where position needs to be defined accurately such as controlling the rudder on a boat or moving a robotic arm or robot leg within a certain range.
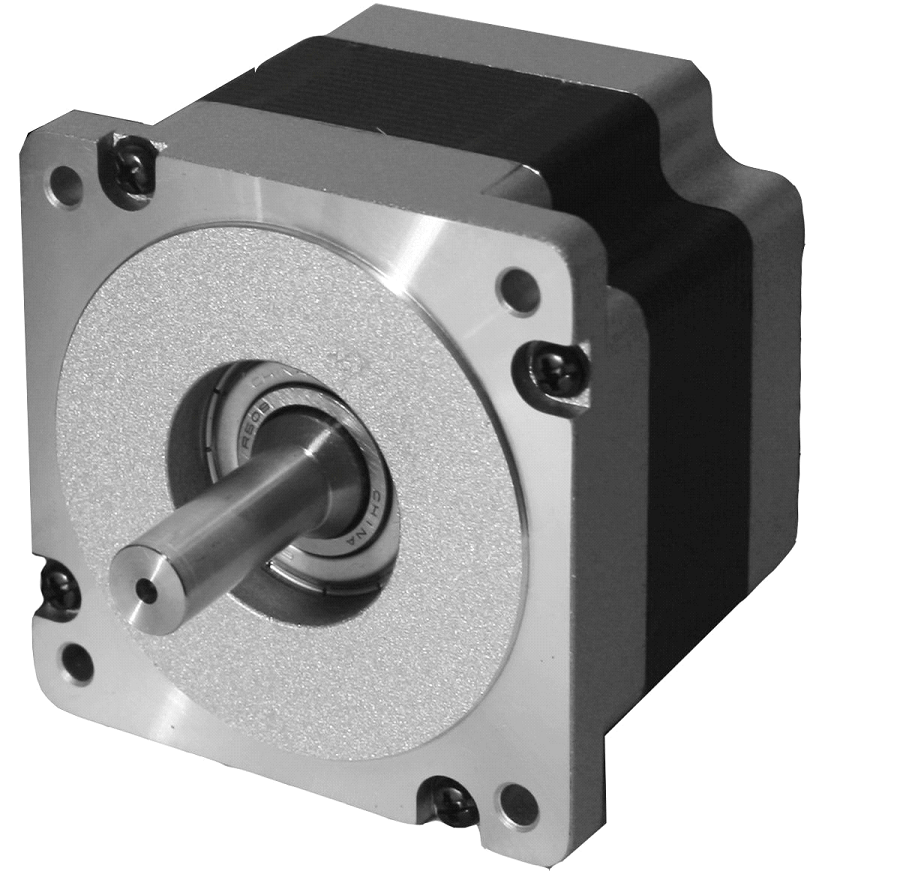
Stepper motor use between 50 to 100 pole to generate an electric current. Stepper motors can accurately move between step position without the need of encoder due to its high number of poles in motor. Stepper motors require an external control circuit or a micro controller to individually energise each electromagnet and make the motor shaft turn. When electromagnet ‘A’ is powered it attracts the gear’s teeth and aligns them, slightly offset from the next electromagnet ‘B’. When ‘A’ is switch off, and ‘B’ switched on, the gear rotates slightly to align with ‘B’, and so on around the circle, with each electromagnet around the gear energising and de-energising in turn to create rotation. Each rotation from one electromagnet to the next is called a “step”, and thus the motor can be turned by precise pre-defined step angles through a full 360 Degree rotation.